MOKUBA by Kitajima Chisaki, Shiraishi Naoya, Hamaue Yuki, Yanoo Sazan
Kyushu University | Graduate School of Human-Environment Studies / Graduate School of Design Studies
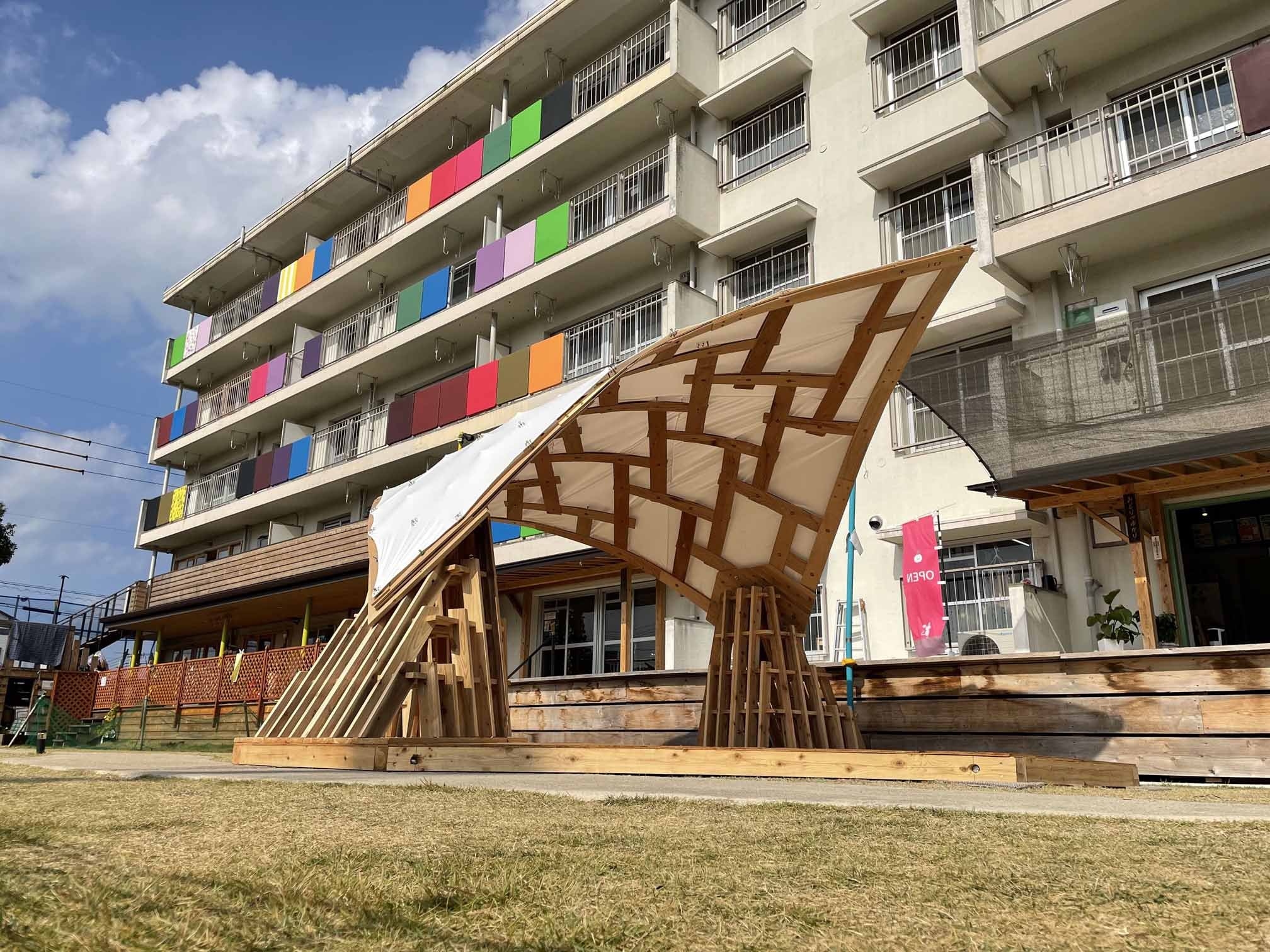
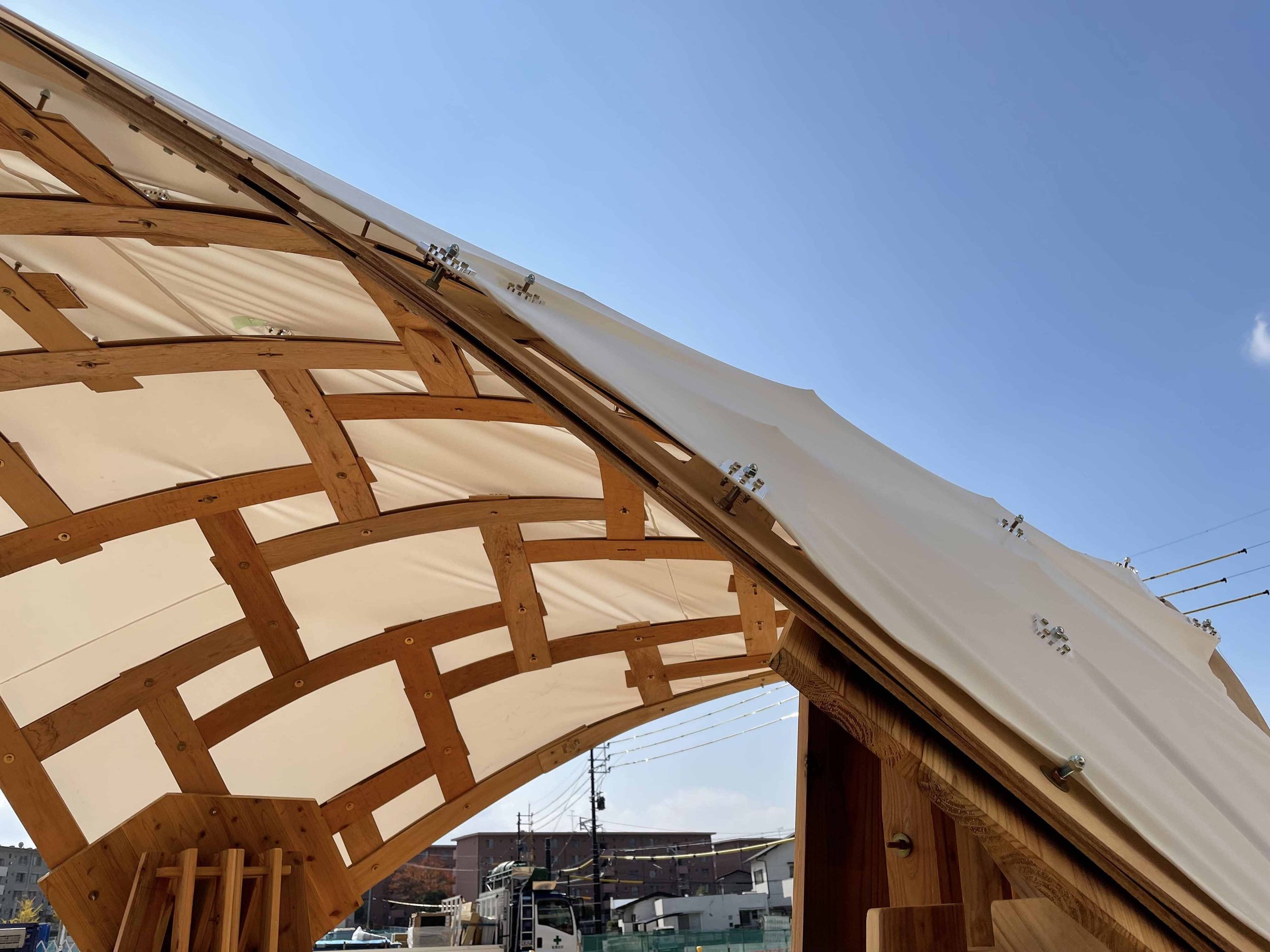
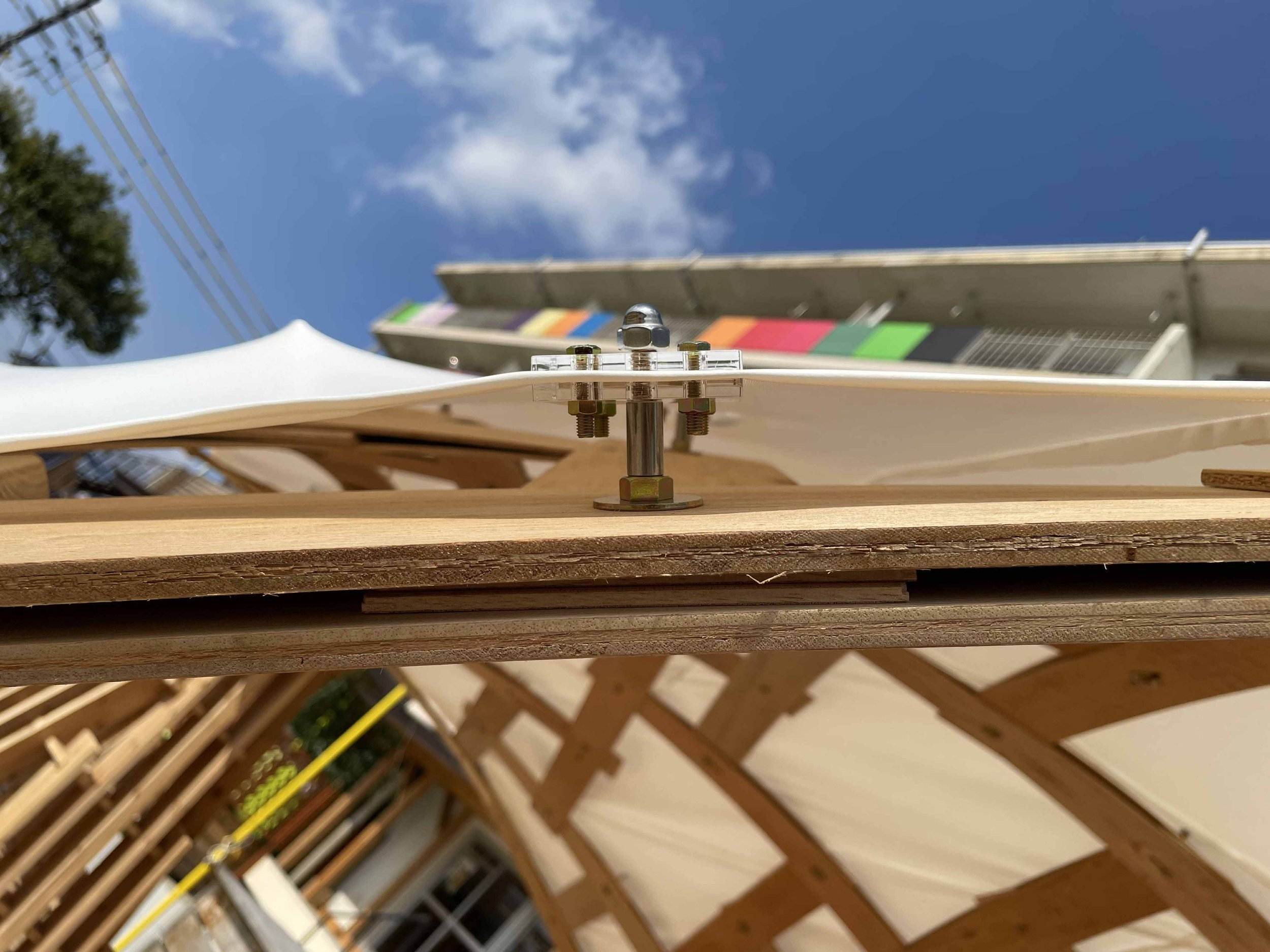
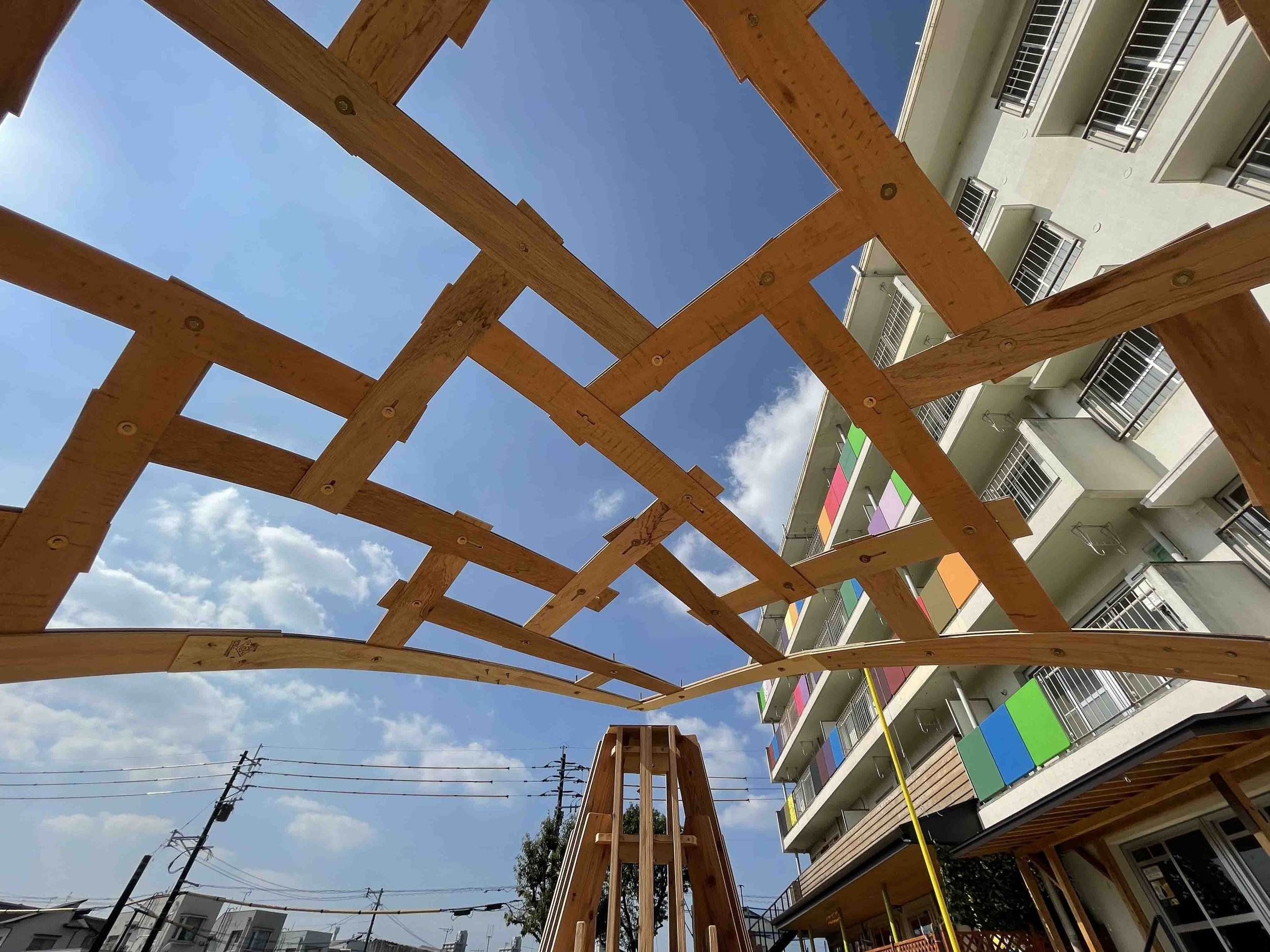
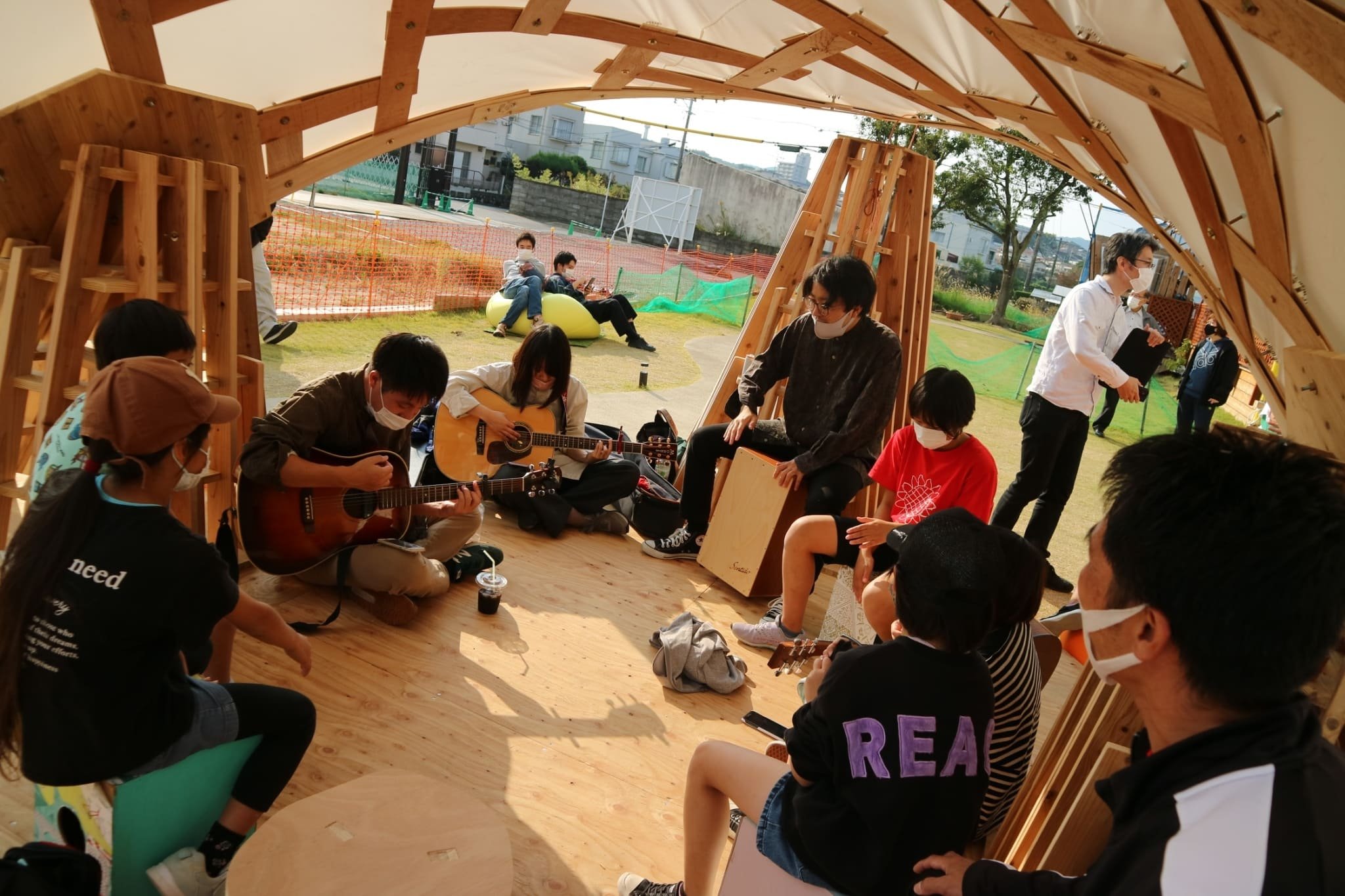
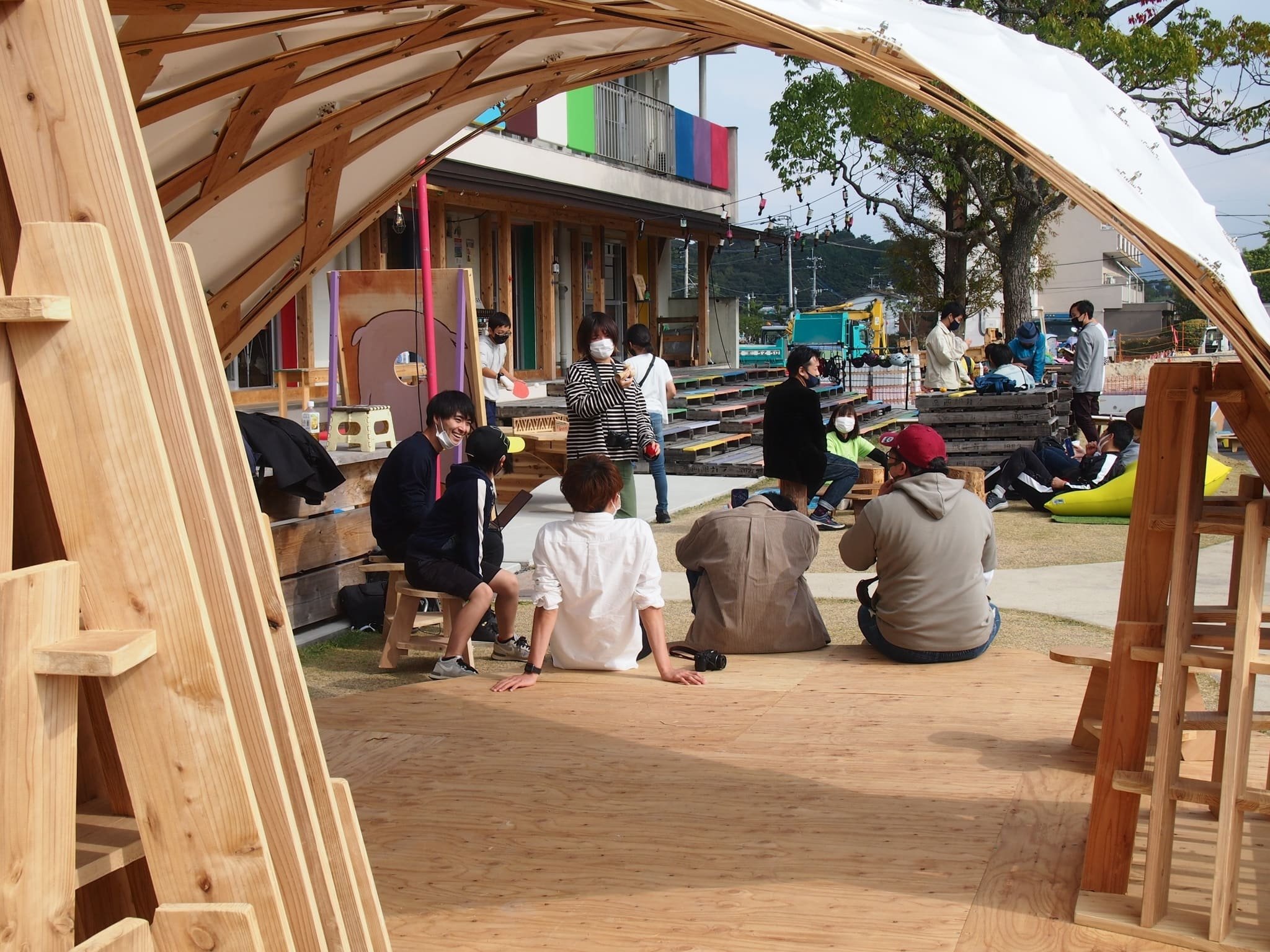
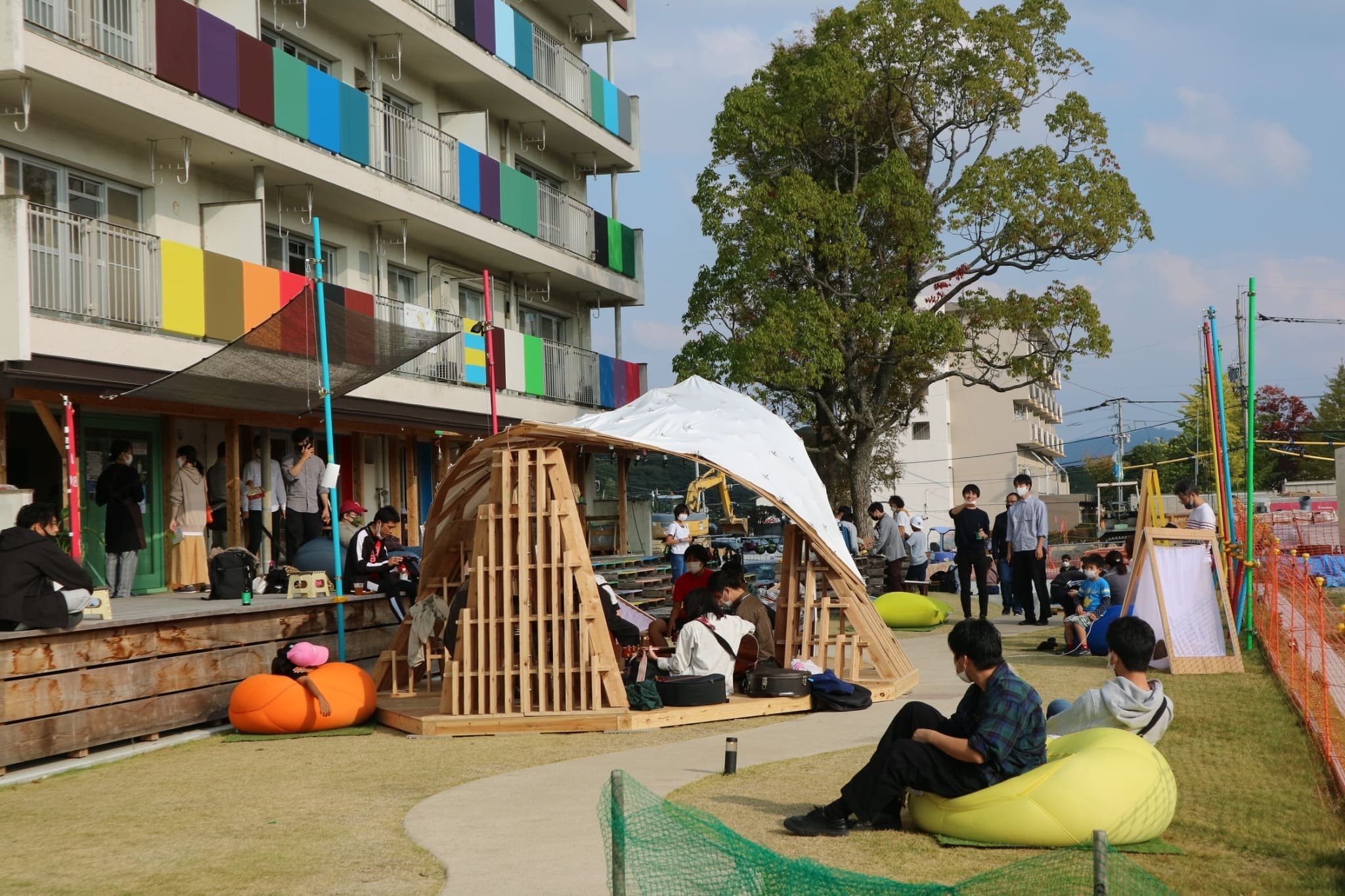
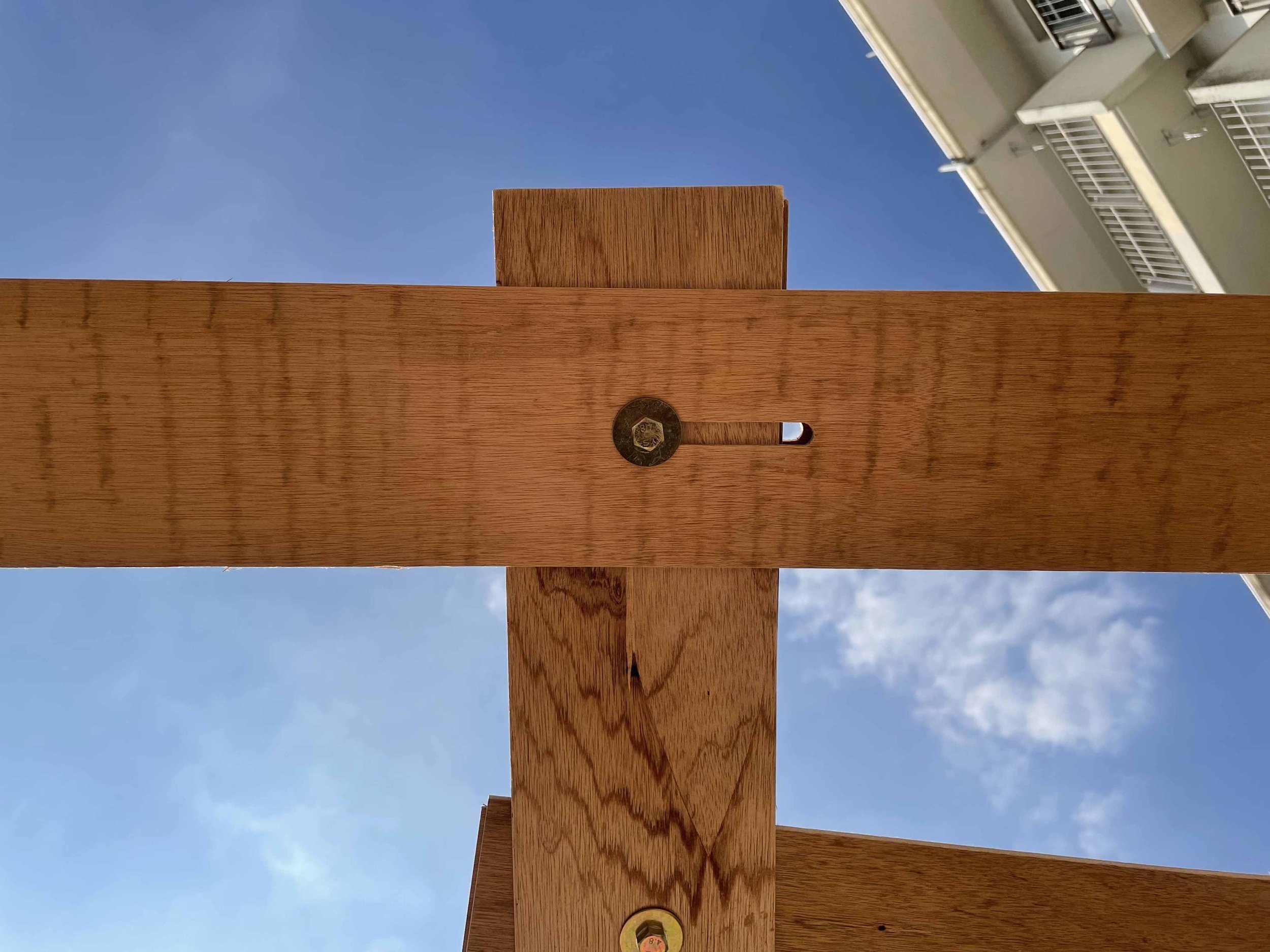
Reciprocal frame structures are structural systems that are formed by the mutual support of components.
We proposed a reciprocal frame structure that has sliding joints and can be deformed from both planar and curved surfaces by elastic deformation of the beam-assembly planar members.
For the realization of the frame structure production, a program was created to generate a geodesic grid that can be deformed into a non-deformable curved surface shape by pulling the two end points by inputting the curved surface shape in accordance with the design intent, and to automate the member numbering and placement as processing data.
For the practical application of reciprocal frame structures. There are two issues: the high degree of difficulty in quantifying the beam assembly and the tendency for errors to occur during construction. To address these issues By introducing a design method that allows deformation to curved surfaces, it is possible to take workability into consideration at the design stage, and three development possibilities were demonstrated: (1) simplified construction, including on-site assembly and removal of pre-unitized units, (2) more flexible curved surface shape design, and (3) transportation in units.
As an operation performed in realizing this structure, two layers of thin plates were used to satisfy both the bendability and strength of the component beam assembly. By sandwiching the ends of the beam assembly between each other when constructing the structure, a structural system of mutual support is maintained regardless of the curvature of the curved surface after the final deformation. A CNC wood tri-axis milling machine ShopBot was used to process the beam assembly members, and the materials used were ordinary plywood with thicknesses ranging from 4 to 9 mm.
For the sliding joints, all bolt travel distances were calculated on the computer based on the positions of the nodes in the flat and curved states. Since the parts all have different joint part data, the exact path to slide in ShopBot and each part number was cut.
Since one of the characteristics of the reciprocal frame is that a large span can be obtained with short and small members, all the beam assembly components were made to fit into 3'6 plywood to keep within the constraints of the machine's machinable size.
The membrane material, which was given the role of a shade, was lifted slightly from the frame by lengthening the bolts at the joints and sandwiching them with acrylic. This allows the pattern of the reciprocal frame in the evening scene to emerge. In addition, the membrane material was devised to be able to be divided by simulation so that it can cover the curved shape of the non-expandable surface by using its elasticity.
The beam assembly made of thin plywood of wood material constitutes a reciprocal pattern, and the name "MOKUBA" is derived from the way the light space, like a bird's wings, expands from its closed flat state to a large space.
words: Kitajima Chisaki, Shiraishi Naoya, Hamaue Yuki, Yanoo Sazan
CREDIT
title: MOKUBA
student name: Kitajima Chisaki, Shiraishi Naoya, Hamaue Yuki, Yanoo Sazan
school: Kyushu University, Graduate School of Human-Environment Studies / Graduate School of Design Studies
year: 2022
category: Installation